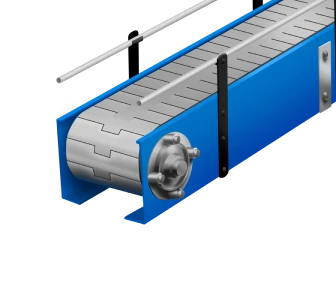
Conveyor systems for poultry farms are used to automate and optimize the processes of cutting and packaging of products. This increases the economic efficiency of poultry processing plants.
Conveyor systems for poultry processing plants are developed taking into account the specifics of technological operations: processing, freezing and packaging of poultry meat.
Higher hygiene requirements are due to the large number of areas where raw poultry meat is handled. The design of our conveyor systems requires fast and complete cleaning as well as operation at extremely low temperatures.
KS SPBelt, mesh, chain, spiral conveyors, as well as conveyors with modular belt and roller conveyors are used in poultry processing plants.
Conveyors KS SPBelt are used in technological processes of primary and deep processing of carcasses:
To ensure food safety, hygiene and technical aesthetics, KS SPBelt conveyor systems have a hygienic design, which reduces cleaning time and the risk of microbiological contamination of products.
We produce conveyor systems taking into account the peculiarities of production, specificity of premises, including non-standard equipment according to customer’s drawings..
The company KS SPBelt is also a Russian manufacturer of modular belts made of special materials with antimicrobial properties. These belts are used at poultry processing plants to suppress the reproduction of microorganisms.
We go to the enterprise, select a solution taking into account the customer's tasks, the characteristics of the transported product and the technological process. We draw up a technical specification and prepare an estimate.
We are developing a technical solution, performing 3D modeling and engineering calculations. We are approving the project with the customer.
At the request of the client, we equip the conveyors with additional equipment and make adjustments. automated control of conveyor lines.
We carry out installation and commissioning, service, warranty and post-warranty service
We are training operators for subsequent pipeline maintenance